An in-depth look at the science, materials, and production process secrets of goalkeeper gloves…
Part One - Material Science
In the last 50 years, the science behind goalkeeper gloves has evolved rapidly. The technological developments behind improving gloves have been influential in shaping the products for goalkeepers in recent times.
The use of modern materials, such as latex and polyurethane foam, has made goalkeeper gloves better quality and safer for use. In particular, the introduction of latex in the 1970s was a revolution.
Today, designers and companies continue to find new ways to utilise latex when it comes to developing the science of goalkeeper gloves.
William Sykes created the first pair of goalkeeper gloves in 1885, which were made from leather and a rubber fitting and manufactured in India. Cotton was also used in the 1940s and 50s before goalkeeper gloves became commonplace.
Sykes’ early gloves didn’t catch, on and were never produced on a large scale. In addition, the later cotton-based gloves were not an ideal material for shot-stopping or handling as the material is absorbent and slippery.
Eventually, latex rubber emerged as the best fit for modern goalkeeper gloves. German brand Reusch was the first known company to use this material when producing gloves after taking inspiration from the stickiness of medical latex gloves. In 1973, the producer worked with former German goalkeeper Sepp Maier to develop the first pair of gloves that used latex on the palm.
While the addition of latex was the biggest modern technological development to improve goalkeeper gloves, many different materials are used in the makeup of gloves today. Modern goalkeepers gloves are generally made from the following materials.
Latex
Latex is a rubber-like material that has a natural chemical makeup of approximately 40% rubber and 60% water. Latex is sturdy and flexible so it is both waterproof and shock-absorbent. But the elasticity of latex ensures it can take a serious impact from the football without impacting its shape.
This material can be harvested naturally from the rubber tree, which is found in South America and South East Asia. Latex comes from the thick, liquid sap that forms underneath the bark in rubber trees. It can be harvested through tapping, where the bark is taken from the tree, and peeled back until the milky-white liquid drips out. This is collected in the first stage of latex production.
Once the bark is tapped, the latex is collected in drums and distributed to its next destination, Then, producers will smoke the latex and add acid to the material. A clumpy fluid will form and this will be rolled into large sheets to remove any remaining water.
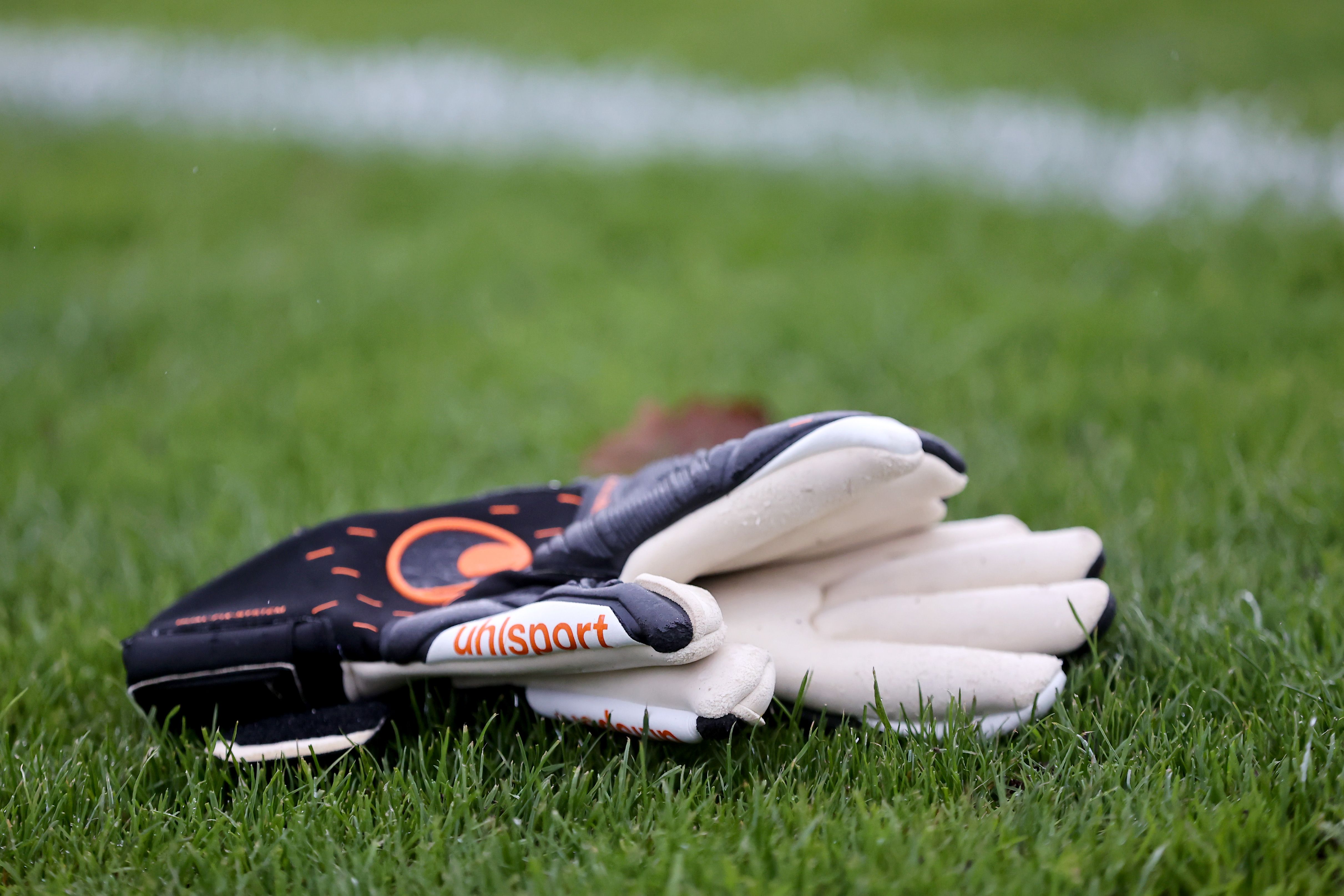
Once dried, these sheets will be prevulcanized, where the sheet is heated consistently at a low temperature so it binds the molecules and creates a durable mould. Further chemicals, such as sulfur and zinc oxide, are added to improve the rubber-like qualities of the latex.
When produced naturally, latex is a sustainable material. Tapping does not require trees to be cut down. Furthermore, once the bark of a rubber tree has been completely tapped, it will regrow and produce more latex sap within a few weeks.
However, in the 20th and 21st centuries, more synthetic, man-made latex is being used from petroleum-based materials styrene and butadiene, a colourless gas that is often emitted from petrol-burning cars. These chemicals are combined to create a latex sheet that is clumped and dried, then distributed to producers.
Depending on the end product, man-made latex will go through different production stages, such as compression, injection moulding or extrusion. In some of these processes, the sulfur prevulcanization stage does not always take place and this can impact the rubber-like quality of the latex.
Generally, such production is cheaper and easier to create in large quantities compared to naturally created latex. Neoprene (also known as polychloroprene) is another type of rubber that can be sold in latex form, and can often be found on glove wrist-straps and backhands.
PU Foam
Beneath the latex coating on the palm and fingers of goalkeeper gloves is a polyurethane foam (PU) material. This type of foam is flexible and can be moulded into the shape of a goalkeeper glove for added padding, shock absorption and comfort.
PU is a completely synthetic, man-made material that combines raw materials, such as isocyanates, polyols and additives. These materials are combined at the beginning of the PU creation process, usually in large steel tanks. The amount of isocyanate (also found in paints and varnishes), polyol (also found in mattresses and insulation) or additive is tweaked depending on the required rigidness and flexibility of the PU materials.
Then, the liquid mixture formed in the tanks is pumped into pipes and heated to form the PU material, known as the polymerization process. Once the mixture comes out of the pipes, the PU has formed and it is moulded further by the addition of carbon dioxide.
Because PU foam is completely man-made and un-reliant on natural materials, it is cheap to mass produce. In addition, there are few hazardous or harmful chemicals used in the production process. As a result, when broken down naturally over time, PU is fairly harmless to the environment, despite being man-made.
However, the strong nature of PU foam takes a long time to break down. The initial signs of breakdown, such as discolouration or loss of strength, start to occur within 20-25 years when exposed to natural conditions like rain, heat and natural sunlight.
Leathers, polyester and nylon
These materials provide the finish to goalkeeper gloves, such as stitching, straps, logos and wrist support.
Today, less natural leather is used in most clothing products, and it's very rare to find a goalkeeper glove that uses leather today. In the past, leather came from animal hides, which were then chemically treated and tanned to provide a longer-lasting material.
More synthetic ways of manufacturing leather have lead to lower costs and more ethical production processes. Some of these procedures use modified cotton and fabrics that have been blended with rubbers or PU materials to create faux leather.
While these are not as longer-lasting as natural leather, they have become used more widely due to the cost factor and because of the lesser impact on the environment.
Velcro, which is often used for the straps to fasten goalkeeper gloves, is made from polyester and nylon in smaller-scale consumer products. These materials are also used to create other parts of goalkeeper gloves, like stitching. Polyester also often forms the majority of the backhand material in a goalkeeper glove. Adidas' recent Predator Pro and Speedportal Pro models' backhands are composed of about 91% polyester, for example.
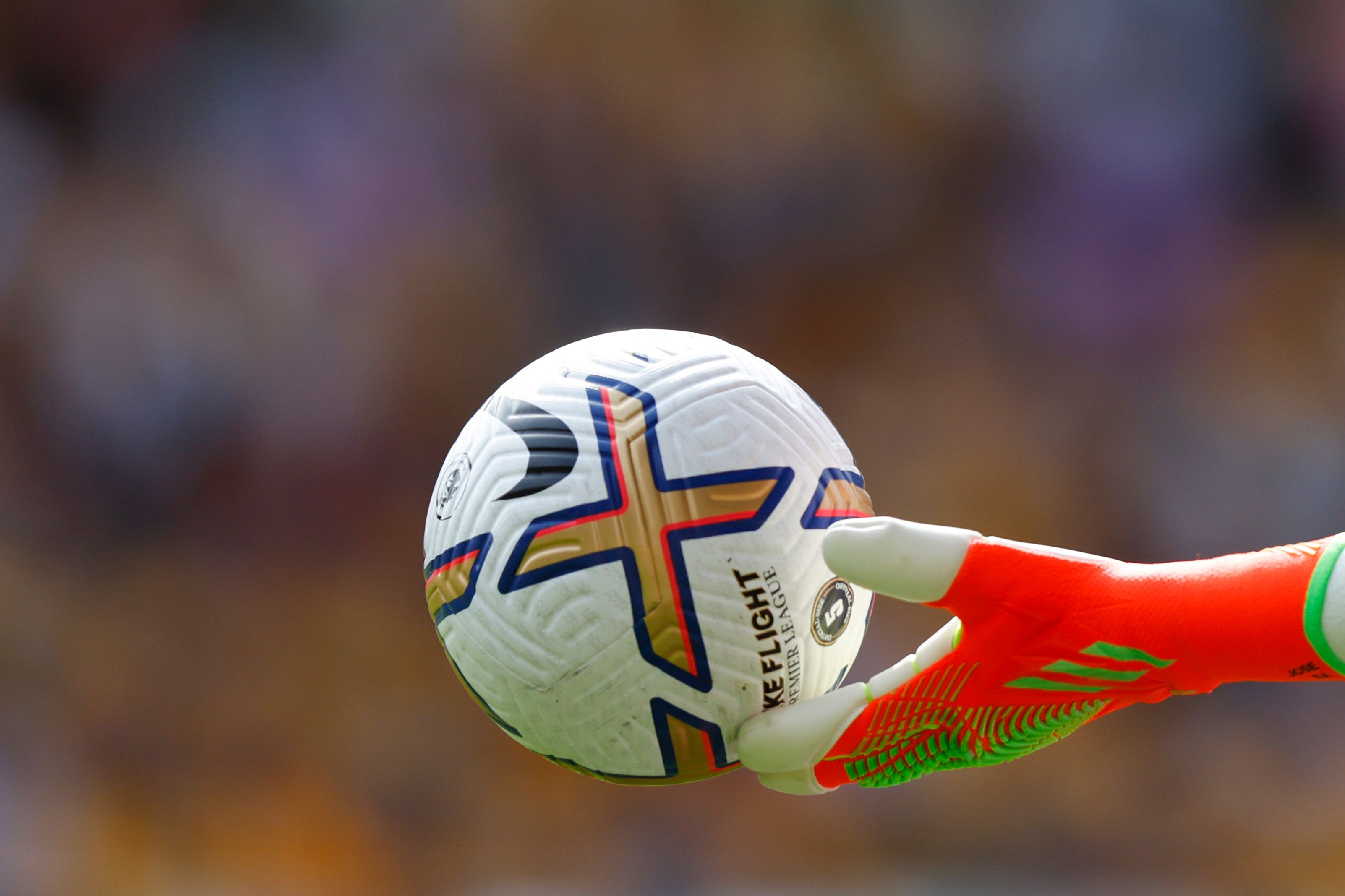
Despite this, Adidas are keen to point out that their new Speedportal Pro models use a blend of renewable and recycled materials that make up about 50% of the material bill of the product.
Both polyester and nylon materials are man-made. Polyester is formed through melt spinning, where the ingredients of petroleum derivatives, air, and water are spun, cooled and hardened. The end product is a plastic thread-like material that is strong but can be re-moulded if necessary.
Nylon is similarly formed from a combination of carbon-based materials, such as coal and petroleum. Through the condensation polymerization process, which heats and applies pressure to the original materials, nylon is processed in a large sheet of melted fibres. The end product is an elastic, strong, but flexible material.
Due to the strength and petrochemicals used in the production of nylon and polyester, both have a substantial impact on the environment. The two items are difficult to degrade and both can emit dangerous gasses. For instance, nylon can emit nitrous oxide during the breaking down process, which is 310 more damaging compared to carbon dioxide.